May 2021
When a phone or computer dies, its usefulness is far from spent. As demand for technology increases, so does the strain on the Earth’s natural resources, specifically the supply of precious metals. The batteries that power our technology—those little lithium-ion ones they ask you about when you board an airplane—are full of metals that can be extracted and reused. Improving materials recycling methods has become increasingly more significant in the mining community, and UArizona experts are on the forefront of that research.
“The lithium-ion market is expanding, nowadays. The lithium-ion battery is used in our portable devices and also, more importantly, in electrical vehicles and storage,” says Jiajia Wu, a PhD student in the Department of Mining and Geological Engineering. “It’s not only consumed by our electronics, but more broadly it is a way to store our energy.”
Wu’s research involves the use of organic acids to extract metals like lithium, cobalt, manganese, aluminum, and nickel from lithium-ion batteries that have already been used up and discarded. The batteries in many electronics tend to have a relatively short lifespan, but the metal used to make them tends to be of really good quality, even after they’re spent. While natural resources, like ores, require a lot of refining to produce useful metals, that work has already been done for ‘urban resources’ like phones and computers.
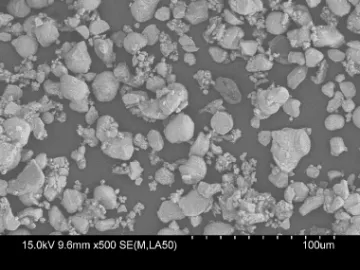
Jiajia WuLiCoO2 in 500x magnification
Jaeheon Lee, Associate Professor of Mining and Geological Engineering and Wu’s advisor, says that: “In terms of urban resources, the grade of gold, silver, platinum, copper, nickel, cobalt—it’s at least a couple orders of magnitude higher than the natural resources. These days, lithium and cobalt are essential to manufacturing batteries.”
Hydromet vs. Pyromet
The techniques used to reclaim metals from things like spent batteries are similar to those used to extract metals from natural ore. “There’s no knowledge gap between the waste and the mines,” Wu says. “It’s the same for the ore and for the secondary resources, the secondary resources being e-waste or spent batteries.”
One method, Pyromet, involves using enormous amounts of energy to burn materials. This method has the downside of releasing harmful chemicals like carbon dioxide, sulfur dioxide and nitrous gas into the air.
Wu chose to experiment with a Hydromet method, which houses the chemical reactions in an aqueous solution. Once the battery is dismantled, acids are added as a ‘leaching agent’ to pull the metals out of the mixture. This is also the preferred method for many industrial applications because the solution makes the process easier to control, and since it doesn’t release toxic gasses it’s safer for workers and better for the environment.
Environmental impact is a critical factor of Wu’s research. She chose her leaching agents, methanesulfonic acid (MSA) and citric acid, because of their impressive ability to extract valuable metals, but also for their biodegradability. Wu has hopes that the acid leaching agents themselves can also be recycled across multiple uses.
Challenges to overcome
According to Lee, the most difficult part of the process is collecting items for recycling. The US doesn’t really have a formal system to do large-scale ‘urban mining,’ and the initial cost of setting up recycling plants can be dauntingly high.
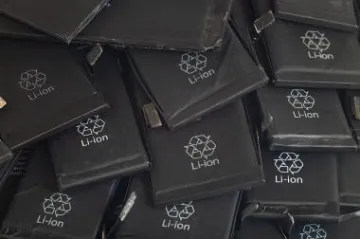
He, along with colleague Hongyue Jin, recently launched a new scientific journal called “Clean Technologies & Recycling.” The journal will focus on disseminating knowledge and educating the public on relevant materials recycling and safe waste disposal.
“Getting the resources, collecting all those cell phones, TVs and computers sitting in somebody’s house is a key factor,” Lee says. “Even in my house in different drawers, I bet I have at least a half dozen cell phones.” Assuming that a proper collection system is established, further obstacles can arise during the extraction process. “What I did is really just a small component in the whole battery cycling process. After we get a spent battery, we have to discharge it. Then we do a physical separation, dismantle it and separate every component individually,” Wu says. “After that, we can use the cathode part to do the metal extraction.”
Both the physical separation and metal extraction are still primarily completed by hand, and Wu is working on finding ways to streamline the process. The end goal is to find the fastest and most efficient procedure that also maximizes how much material is reclaimed. “For the nickel, cobalt and manganese, they behave really similarly as elements. Their properties in terms of solvent extraction and precipitation are pretty similar,” Wu says. In other words, it sometimes takes five or six separation stages to fully extract the metals, a portion of which are lost along the way.
Regardless, Lee and Wu are both optimistic that their research and that of others in the field will lead to great success in recycling mineral resources. “The technology is there,” Lee says.
Jiajia Wu Wins Best Student Paper Award at MPD Conference
For her paper on the research described above, Jiajia Wu was awarded Best Student Paper Award at the Minerals Processing and Metallurgy Division of Colorado meeting in June 2021.