April 2021
Imagine opening a burning oven and feeling that wave of hot air escaping into the room. Then, imagine a work environment where extremely high temperatures are not only normal, but constant. Warmed by the natural heat of the Earth, conditions in deep underground mines are an entirely different ballgame than the cooler, shallower caves most people are familiar with.
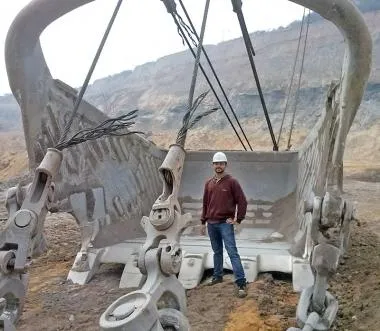
Mohit Butani
UArizona graduate student Mohit Butani is exploring ways to protect workers and reduce costs by making heat management in mines about prevention rather than mitigation. “The basic problem in deep underground mines is as you go deep into the ground, you basically end up having a lot of geothermal heat and that causes the air temperature and the ground temperature to rise,” Butani says.
Temperatures underground increase by 72-87 degrees Fahrenheit per mile of depth, mostly due to that geothermal heat. Other factors, like machinery, mechanical processes and the metabolic heat created by people moving around, make it so the average temperature in some mines reaches 125-130 degrees.
When workers are exposed to such high temperatures for long periods of time, they may begin to experience heat stress, rashes, cramps, and heat exhaustion or stroke. Some may even develop heart and lung diseases. Needless to say, there are good reasons why ventilation and cooling comprise nearly a third of operational costs in the mining industry.
“The cost that goes into cooling down the mines to maintain a workable environment is astronomical, because cooling the whole mine using just ventilation is a pretty costly affair,” Butani says. “The best way to prevent that would be something to just quickly prevent the heat from getting in the mines, right?”
Laying out the options
Alternatives for heat management generally fall within a few categories: fans and ventilation, water cooling, wearable items (like vests and watches), or prevention.
Butani’s research involves a preventative method called direct foaming, where specially formulated porous foam is applied to the mine walls. The foam works like insulation in home construction, but instead of keeping the warmth from escaping, it is used to keep the heat on the outside. Less heat entering the mine decreases the need for cooling and reduces the overall cost of keeping operations safe for workers.
Heat travels easily through less porous materials like rock and metal but bounces around when it runs into air pockets. According to Butani, this quality makes air an exceptionally good insulator. The same technique is used for climate control in cold environments, including the double-pane windows that help keep buildings warm in Antarctica. Even better, the materials needed to create this foam—primarily silicon, aluminum, and oxygen—can be found right in the mine’s tailings. “The mine tailings are basically the wastewater that comes out of the mines after all the chemical processing it goes through. There are tailing ponds that let the water evaporate,” Butani says. Whatever minerals are left behind can be collected and recycled for use in the foam.
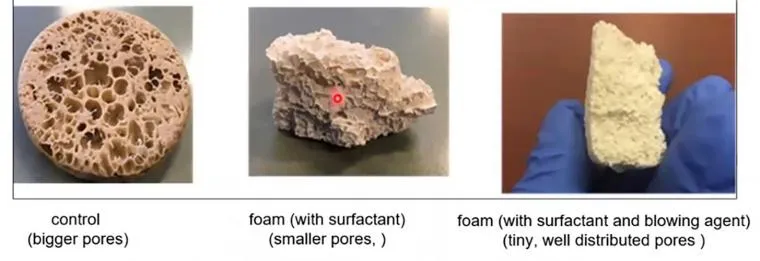
Foams with various pore sizes
A foam that’s just right
After combining the tailings minerals into a ‘ceramic slurry,’ Butani went on to the next phase of his experiment: calculating the ideal ratios for the most useful foam. He used hydrogen peroxide to make the mixture porous and stearic acid to stabilize the bubbles. With the help of established software like the LAMMPS Molecular Dynamics Simulator, he was able to save a lot of effort and funding to find the most ideal ratios.
“Simulations are easy. Simulations take less time,” Butani says. “We did create a lot of samples in the lab as well, but it’s not possible to do all of the analysis on the actual physical experimental samples that we have, so we’re using simulations to cut down on that time.”
Once the simulations find a ratio that has promising results, Butani can create the physical sample for further testing. The end goal is to create a sample with maximum porosity that is still strong enough to withstand the elements, since a higher porosity means more air pockets for the heat phonons to engage with (and a better performing foam). He plans to continue looking into more porosity and density combinations in the future.
“If this is something that will reduce the overall environmental impact and improve efficiency, it will save money for the mines to operate. On top of that, it improves the efficiency of people working in the mines because the temperatures are much cooler,” Butani says. “That’s a triple win-win situation.”
Butani presented his research virtually at the MineXChange 2021 SME Annual Conference & Expo.
On Mohit Butani
Mohit Butani received his bachelor in Mining Engineering from the Visvesvaraya National Institute of Technology Maharashtra. Following that, he worked at multinational mining company Vedanta Resources for two years. As an Assistant Manager, he was involved in an upscaling project for a new Bauxite mine. He joined UArizona in the fall of 2019 for his Master of Science in the Mining and Geological Engineering department, which he completed in 2021.