November 2021
This is a summary of this year’s Mining Law Summit opening talk by geologist and engineer Dave Hammond and Dr. Roderick Eggert, expert for critical materials. The recording of this dialogue is available at the Global Mining Law Center YouTube channel.
What are the critical minerals and materials?
Three fundamental characteristics apply to all critical minerals:
-
They provide critical functional properties to a product or process.
-
They are, in our current environment, very difficult to substitute for in the products or the functionality that you're trying to achieve.
-
They involve risky supply chains. This could refer to the physical existence of the materials, risky situations along the supply chain where the materials are converted to intermediate or finished products, or the location of all of these components of the supply chain.
There are some additional attributes that don't apply to each and every one of the critical minerals and materials (or CMs, for short), but are very important for some of them:
-
CMs frequently are byproducts from the extraction of other metals or minerals. Presently, a lot of this byproduct material is not recovered and goes into the waste stream.
-
For many CMs, the technologies of turning the raw material into usable forms can be quite challenging.
-
For a number of these CMs, the tonnage involved is currently relatively small, in the range a few thousand to several hundred thousand tons.
-
Some CMs are produced by very small-scale mining operations.
-
In many cases, reserves of such CMs are not quantified as they would be for major metals like copper.
The criticality of mineral materials to the US is also illustrated in the USGS Mineral Commodity Summaries, published yearly. They show the percentage of import for a number of materials, as well as the primary exporters. For 17 materials, from arsenic to yttrium, the US dependency is 100%. For 10 of them, China is one of the major import sources, with Canada and Russia also being important suppliers.
Over the last decade, US policymakers have put a lot of work into critical minerals and materials from the perspectives of defense and of the economy. This is evident particularly on the energy side, and to make the electric power system less carbon-based. The current list of formally defined and identified critical minerals was published in the Federal Register on May 18, 2018 and includes 35 minerals or mineral material groups. (Currently, USGS is preparing a new, extended list with the period for public comment having ended December 9, 2021.)
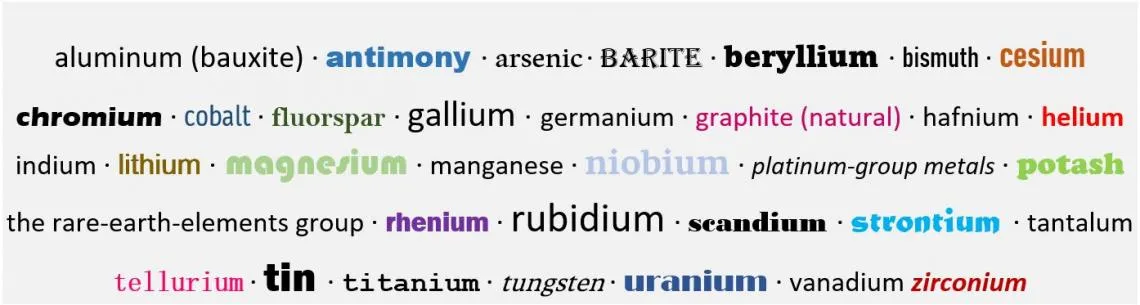
Current list of 35 critical minerals
These elements or families of elements reflect materials that that satisfy two characteristics:
-
there is a significant degree of net import reliance for the United States.
-
there is lack of diversity in the supply chains
Import dependence is a useful initial indicator of riskiness of supply chain, but it's only part of the story. If we have diverse important sources a supply chain may be no riskier than if we have a single vulnerable domestic source. Another aspect of risk is that the lack of certain materials puts the development and deployment of emerging energy technologies at risk. This list reflects risks from the perspective of US manufacturers and customers. Manufacturers that use these materials in components and manufactured systems and the customers, all of us who purchase automobiles, refrigerators, and other electronic equipment.
Critical mineral needs for clean energy technologies (excerpt)
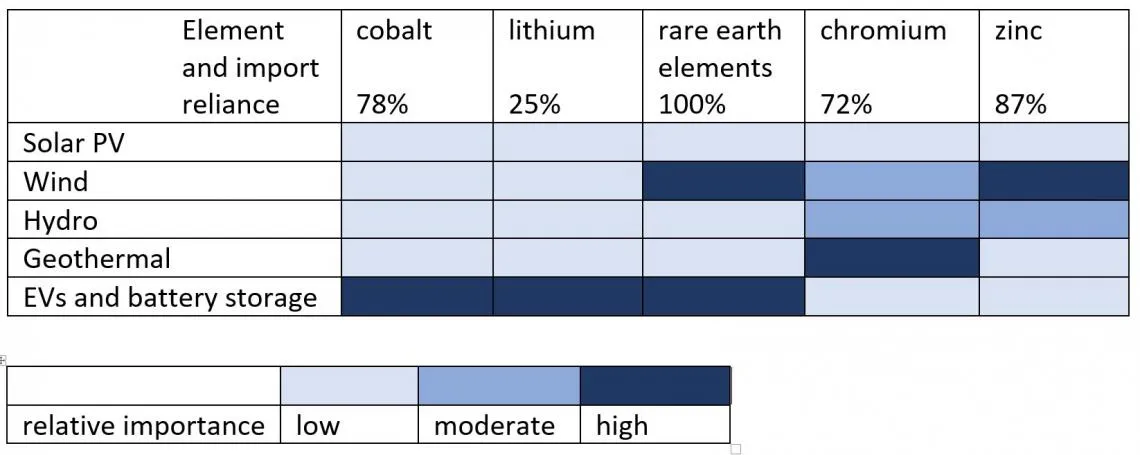
Critical needs vary significantly from one technology to another. Cobalt and lithium are essential in lithium-ion batteries, a device that is for the next couple of decades, if not longer, the battery technology of choice in electric vehicles. Rare earth elements are important in state-of-the-art magnets, which are essential for the most efficient electric motors, which, in turn, are critical for offshore wind turbines, electric vehicles, and battery storage in many electrical generation activities. Chromium and zinc are important materials in specialty steels that are used in the manufacture of wind turbines and hydro facilities.
How do critical minerals differ from other important mineral commodities?
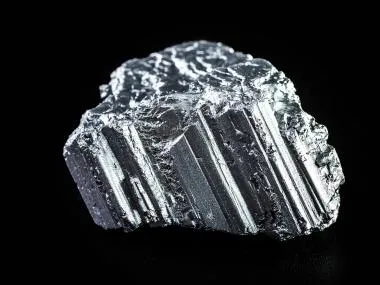
Neodymium, a rare-earth element
Many critical minerals or materials are minor in the sense that the overall annual tonnage produced and consumed is reasonably small. An extreme case would be scandium, one of the elements on the US critical minerals list, which is used in metal alloys. Its annual world production is about 10 tons a year. Copper production, in comparison, is around 20 million tons per year. For lithium and rare-earth elements, the numbers are around 200,000 tons per year. In that sense, critical materials are like vitamins and spices: in small quantities they provide central functions.
Many of the minerals turned critical are produced largely or, in some cases solely, as byproducts or in association with other relatively more important materials (from the perspective of the mine operator).
Some of these minor metals are not financially attractive to a major mining company because they don't contribute significantly to their bottom line. However, a growing number of junior mining companies are getting involved in materials such as the rare earths and lithium. This brings in a whole host of considerations for a policymakers and investors: their capitalization and ability to finance, does the company have the expertise to deal with oftentimes very complex mineralogy and, more importantly, the very hard technology that's required to process these minerals into their marketable form?
The production technology for major metals has been around for thousands of years and has evolved to very efficient and economical processes. With some of the minor metals, the technology is still in the early stages of development. For a lot of these metals, the technology is much more complex. In the case of rare earths, instead of having one or two primary metals and possibly a byproduct metal, you're dealing with sometimes 5-10 individual rare earth elements that you want to extract, and so the distillation process becomes incredibly complex. Companies have different approaches, and often they try to develop their own technologies, which may or may not be proven in the end.
Manufacturers strive to make their supply chains less risky by forming strategic alliances. They, for example, guarantee that they will buy a certain fraction of a new mine’s output. This agreement allows the mining company to raise capital on the financial markets, because the investors are confident that at least some of the output has a guaranteed market. In some cases, manufacturers are co-funding investments in mining and mineral processes.
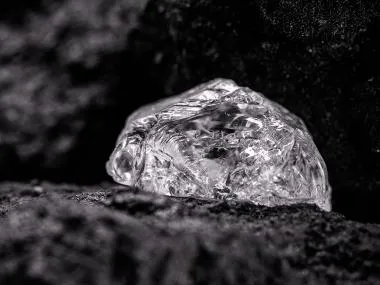
Petalite, also called castorite, an important source of lithium
The larger manufacturers also undertake R&D to eliminate or at least significantly reduce their need for certain critical materials. For example, they have initiatives underway to develop magnets that don't require what are perceived to be risky rare earth materials.
Could we achieve independence from supply chain risk by developing resources here in the US?
The ability to become self-sufficient varies somewhat from mineral to mineral. Some of these materials simply aren't found in the US. What’s needed are diversified, secure, and sustainable supply chains. Additional domestic mineral production is only one part of this. A promising combination could be “re-shoring,” i.e., relocating activities back to the United States, “near-shoring,” i.e., getting stages in the supply chain closer to us, like Canada or Mexico, and working with allies. Thus, diversified supply chains can be created, that reduce the risk of a single point of failure. That could be of geopolitical nature, weather- or climate-related, a natural disaster, or it could be the shipping disruption risk.
How to balance the desire for low costs at the moment and the security from disruption is a question that policy makers need to give serious thought to.
The Presenters
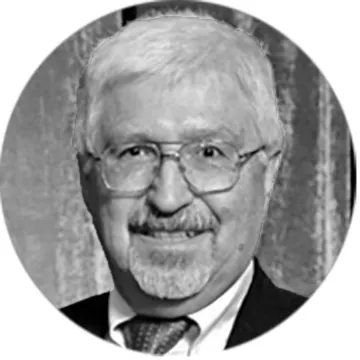
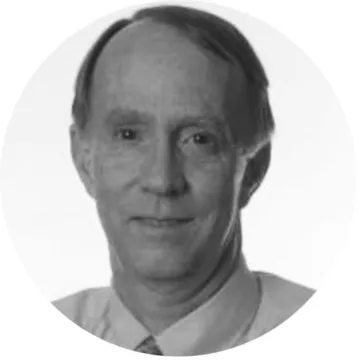
David Hammond
Geologist, engineer and mineral economist with over 45 years experience in the natural resource industries. He has been involved at one time or another with almost every energy and mineral commodity.
Roderick Eggert
Geochemist turned economist, he is professor and former director of the Division of Economics and Business at the Colorado School of Mines and deputy director of the Critical Materials Institute
More information
USGS Mineral Commodity Summaries 2020, contains information on the US net import reliance for a number of minerals
IEA, The Role of Critical Minerals in Clean Energy Transitions, May 2021